Surface Mount Technology (SMT) stands at the forefront of electronic manufacturing, revolutionizing how components are mounted on circuit boards. Widely embraced for its versatility and compact design, SMT has become a cornerstone in the electronics industry, offering enhanced efficiency, reduced size, and heightened reliability in electronic assemblies. This introduction delves into the widespread adoption and key advantages that make SMT a driving force in electronic manufacturing.
OSAT Explained: The Engine Driving Semiconductor Innovation.
What is SMT?
SMT, or Surface Mount Technology, is an electronic assembly technique where components are mounted directly onto the surface of a printed circuit board (PCB). This method contrasts with through-hole technology, offering advantages like smaller size, increased component density, and improved production efficiency. SMT is widely used in electronic manufacturing for its versatility and ability to meet the demands of modern, compact electronic devices.
Operating Principles of SMT.
Surface Mount Technology (SMT) operates on the fundamental principle of directly attaching electronic components to the surface of a printed circuit board (PCB). The key operating principles include:
- Component Mounting:
- Adhesive or Solder Paste: A thin layer of adhesive or solder paste is applied to the surface of the PCB where components will be mounted.
- Pick-and-Place:
- Automated Placement Machines: Precision pick-and-place machines accurately position components on the solder or adhesive, guided by a digital blueprint of the PCB.
- Reflow Soldering:
- Heat Application: The assembled PCB is subjected to controlled heat in a reflow oven, causing the solder paste to melt and securely attach the components to the board.
- Component Size and Density:
- Miniaturization: SMT allows for the use of smaller and more closely spaced components, contributing to the overall reduction in the size of electronic devices.
- Elimination of Through-Hole Technology:
- Direct Mounting: Unlike through-hole technology, SMT eliminates the need for drilling holes in the PCB, enabling components to be mounted directly on the surface.
- Increased Efficiency:
- Automated Processes: SMT leverages automated assembly processes, enhancing production speed, precision, and overall manufacturing efficiency.
Understanding these operating principles provides insight into the streamlined and space-efficient nature of SMT, making it a cornerstone technology in contemporary electronic manufacturing.
Advantages of SMT.
- Flexibility:
- Diverse Component Compatibility: SMT accommodates a wide range of component sizes and types, offering flexibility in designing intricate electronic circuits.
- Size Reduction:
- Compact Design: By eliminating the need for holes in PCBs, SMT contributes to a significant reduction in the overall size and weight of electronic devices.
- Higher Component Density:
- Increased Integration: SMT allows for higher component density on a PCB, enabling the creation of more powerful and feature-rich electronic assemblies.
- Improved Electrical Performance:
- Reduced Signal Interference: The shorter distances between components and the elimination of through-holes result in lower parasitic capacitance and inductance, enhancing electrical performance.
- Enhanced Production Efficiency:
- Automated Processes: SMT leverages automated assembly, pick-and-place, and soldering processes, leading to faster production cycles and increased throughput.
- Cost-Effectiveness:
- Material Savings: SMT reduces material usage, lowers production costs, and minimizes waste, making it a cost-effective choice for electronic manufacturing.
- Reliability:
- Mechanical Stability: Components mounted directly on the PCB are mechanically more stable, enhancing the overall reliability and robustness of electronic assemblies.
- Improved Thermal Performance:
- Enhanced Heat Dissipation: SMT facilitates better heat dissipation due to direct component attachment, reducing the risk of overheating and enhancing the overall lifespan of electronic devices.
In summary, the advantages of SMT encompass increased flexibility, size reduction, higher component density, improved electrical performance, enhanced production efficiency, cost-effectiveness, reliability, and improved thermal performance. These factors collectively contribute to the widespread adoption of SMT in modern electronic manufacturing.
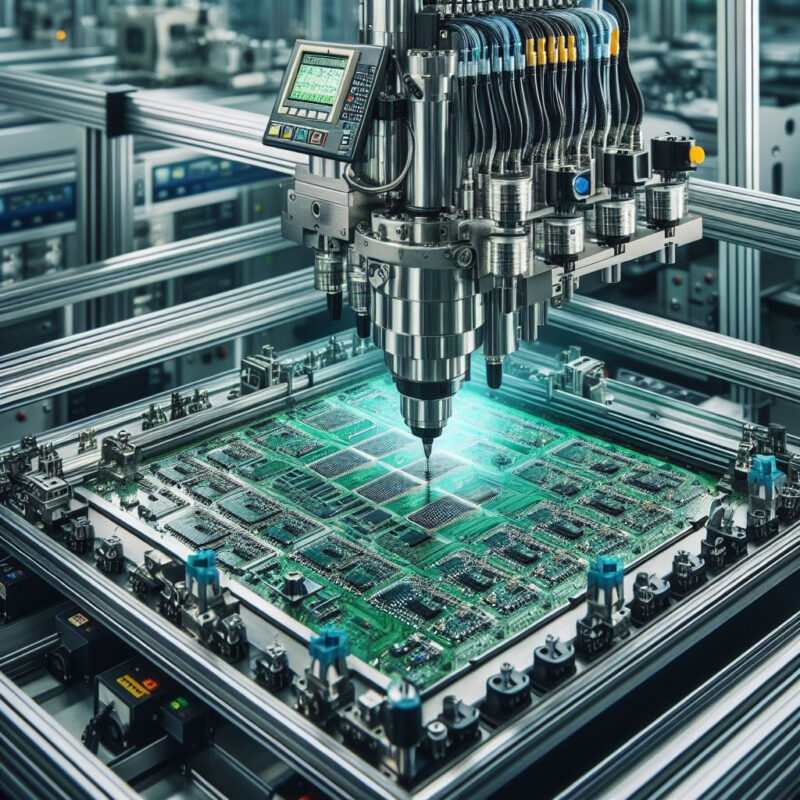
SMT Process.
- Surface Preparation:
- Cleaning and Coating: The PCB surface is meticulously cleaned to remove contaminants. A thin layer of solder paste or adhesive is then applied to designated areas.
- Component Placement:
- Pick-and-Place Machines: Automated machines precisely pick components from reels or trays and place them onto the solder paste-covered areas based on the PCB design.
- Reflow Soldering:
- Heat Application: The assembled PCB moves through a reflow oven where controlled heat is applied. This melts the solder paste, bonding the components to the PCB surface.
- Inspection:
- Automated Optical Inspection (AOI): The PCB undergoes AOI to detect any defects or misalignments in component placement after reflow soldering.
- Secondary Reflow (Optional):
- For Double-Sided PCBs: In cases of double-sided PCBs, a secondary reflow process may be applied to secure components on the reverse side.
- Cleaning (Optional):
- Removal of Residues: If necessary, the PCB undergoes a cleaning process to remove any flux residues left from the soldering process.
- Testing:
- Functional and Electrical Testing: The completed PCB undergoes comprehensive testing to ensure functionality and electrical performance.
- Final Inspection and Packaging:
- Quality Assurance: A final inspection is conducted to verify the overall quality. The PCBs are then packaged and prepared for distribution.
This step-by-step SMT process ensures the precise and efficient assembly of electronic components on a PCB, culminating in reliable, high-performance electronic devices.
Conclusion.
In conclusion, Surface Mount Technology (SMT) stands as a cornerstone in electronic manufacturing, offering a multitude of advantages that shape the landscape of modern circuit assembly. The key takeaways are:
- Efficiency and Precision:
- SMT’s automated processes ensure efficient and precise placement of components, enhancing overall manufacturing speed.
- Compact Design and High Density:
- SMT’s elimination of through-holes allows for a reduction in size and weight, facilitating the creation of smaller, more powerful devices with increased component density.
- Cost-Effectiveness:
- The streamlined processes of SMT contribute to cost savings through reduced material usage, lower production costs, and minimized waste.
- Reliability and Thermal Performance:
- Direct component mounting enhances mechanical stability, increasing overall reliability. Improved heat dissipation contributes to extended device lifespan.
- Versatility and Flexibility:
- SMT’s versatility accommodates diverse component sizes, making it adaptable to a wide range of electronic applications.
In light of these advantages, SMT not only meets the current demands of electronic manufacturing but also holds immense potential for future development. Its role in driving innovation, enhancing production capabilities, and contributing to the creation of more advanced and compact electronic devices underscores the pivotal importance of SMT in the rapidly evolving world of technology.